You’re a new building owner and have been wondering what’s underneath that shiny lid in the yard. More than likely it is a backflow preventer installed in a vault. The backflow preventer is required by the local water jurisdiction to maintain safe drinking water for the community, necessitating the use of a backflow assembly to meet specific requirements and functionality. Domestic, fire sprinkler, and irrigation lines all need some sort of backflow prevention assembly on them, including backflow preventers and backflow prevention devices like reduced pressure backflow assembly (RPBA), which is a common type of backflow preventer used in various settings, and vacuum breakers to protect against backsiphonage. These systems, especially in critical services like hospitals, ensure a continuous water supply without any interruptions, highlighting the importance of cross connection control as a regulatory requirement for backflow prevention.
Maybe you already knew all that and you’re ahead of the curve. Well, here’s what you might not know. Maintaining this equipment can quickly become a challenging headache once installed, emphasizing the importance of professional backflow preventer installation and the decision to install a backflow by a certified professional to ensure the safety of drinking water. Components such as relief valves and shutoff valves play crucial roles in the functionality of backflow prevention assemblies, and considerations for supply pressure are vital during the installation process.
Vaults fill with water without a backflow preventer
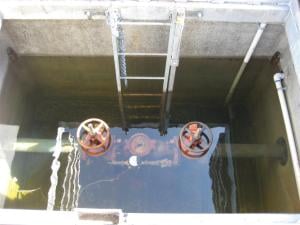
That is actually a huge problem. If the test cocks are covered with water a backflow condition can exist. Drinking water can be compromised, which defeats the purpose of the entire installation. To mitigate this risk, maintaining an air gap between the end of a hose and the surface of the water is crucial to prevent the entry of chlorinated pool water into the drinking water system during a backflow condition. The most common “solution” is installing a sump pump to prevent the vault from filling. A sump pump requires its own maintenance and becomes the device our clean drinking water depends on. Sounds risky to me. Do you really want to have to depend on someone to make sure the sump pump works all the time? Plus, backflow testers tell us over and over that the sump pump doesn’t work - these vaults are still full of water.
Vaults are damp due to faulty shutoff valves
Even in rare cases where vaults don't have flooding problems, they get damp. That's just how it is. Just look at all the crud on and around that valve. This often causes the equipment to rust over time. In addition to this, it also causes the sediment in the bottom of the vault to become wet. You could always have someone try to clean it out, but scooping out the wet sediment is not a quick and simple task. It poses a problem, as damp sediment is slippery. A dark and cramped vault is not a pleasant place in which to slip.
Vaults are a safety hazard for fire sprinkler systems
The Occupational Safety and Health Administration (OSHA) imposes measures such as hoses, tents and extra men in order to legally access vaults for maintenance. They've recently made it even more difficult to get things done in vaults with new regulations requiring a permit for entry into hazardous or potentially hazardous spaces. Most water vaults are included under that heading. The paperwork is not something anyone wants to spend time on. It is a necessary evil, however, as OSHA claims there are thousands of confined space related incidents and about 90 fatalities each year.
Vaults are out of sight
This may go without saying, but vaults are hidden underground. This is their big, shiny redeeming quality - you don't have to look at them.
Enclosures blend in
Enclosures maintain a specific climate to prevent drinking water contamination
Aluminum enclosures can be designed with hot, cold, and wet climates in mind. There are heaters which can maintain 40° Fahrenheit in as low as -30° weather. There are also vents, louvers and fans to keep things cool in moderate climates. Industrial enclosures can even come with full air conditioning units for equipment that produce lots of heat or for use in hot climates. To keep things dry, backflow covers are manufactured with some form of drain. Safe-T-Cover's, for instance, use a drain flap.
Enclosures are easily accessible.
They are designed with maintenance in mind. The highest quality backflow preventer covers are ASSE 1060 approved, which means they've gone through rigorous testing in a number of categories. One of the requirements to pass this standard is to have a lid that opens and locks in place. That means it won't fall on someone sticking their head or arms inside for testing or repairs. Some enclosures have removable panels and doors as well for ease of access. You can even request custom builds that have access doors or cutouts exactly where you need them, like the one pictured here.
What works best for you?
Which would you want to deal with on your property? Think about it – which will require more attention and maintenance - a backflow prevention assembly device often covered with water or one that is installed above ground in an enclosure? Believe it or not, backflow installation should be on your mind. One of the best things you can do to avoid costly problems and halts in production is to listen to the testers or repairmen who work on your equipment. They know the most about dangers and problems associated with vaults because they experience them firsthand.